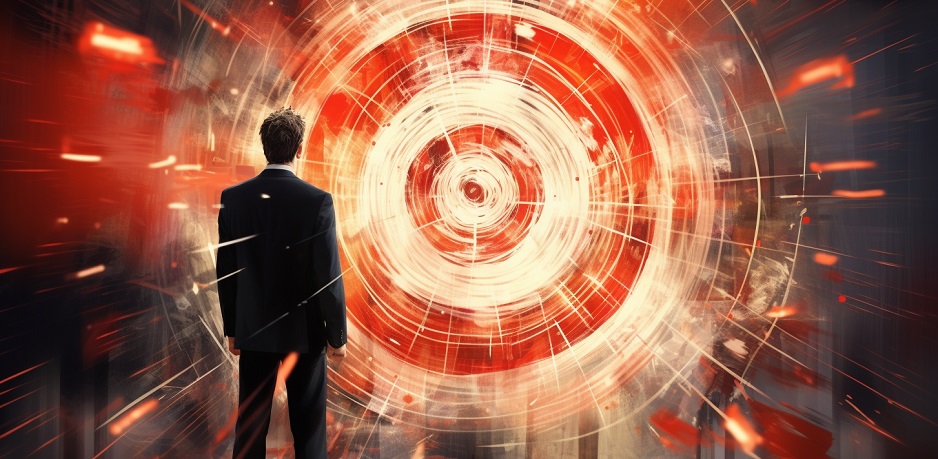
Our Focus
It's very simple; to design and manufacture safe, reliable and affordable lithium-ion and LiFePO₄ batteries.
Radenite is a Coventry-based developer and manufacturer of Li-ion and LiFePO₄ batteries
It's very simple; to design and manufacture safe, reliable and affordable lithium-ion and LiFePO₄ batteries.
We design and manufacture batteries. We are meticulous in how we make these batteries. We start with high quality factory fresh cells from manufacturers like Panasonic, Sony, LG and Samsung. If you want to know more about the techniques we use and can endure technical detail, read on.
Before battery assembly, each candidate cell is charge recycled to ensure it will operate at the correct current and within the specified cut-off voltages of the Battery Management System. The cell is then charged to a specific voltage to match other candidate cells for that battery. Finally, the internal resistance is measured to ensure it's within a safe range of the other candidate cells to be included in battery assembly. If the cells' initial voltages or internal resistances are mis-matched, the battery will underperform. For example, if 9 out of 10 cells in a Lithium Ion 36V 10S1P (10 single cells in series) battery are 3.6V with one at 3.1V, then under load conditions, when this last cell reaches its voltage cut-off threshold (eg ~3.0V), the BMS (Battery Management System) will detect the breach and will cut the connection to load; this despite the overall battery voltage of 34.5V (or almost 40% of available charge left in the other cells).
Likewise, during the charge cycle, cells that have higher internal resistance or lower voltages will not reach full voltage at the same rate as the other cells. If this discrepency is material it can mean that the battery never reaches its full charge potential. For example, just one cell exhibiting a significantly lower internal resistance in a LiFePO₄ battery will result in it reaching full 3.6V charge ahead of the others. A balancing BMS will endeavour to drain some of the excess charge from this cell so that the others may "catch up", but may be unable to prevent it from exceeding its high voltage cut-off threshold. In this situation, in order to prevent cell damage (or in the case of Li-ion batterries, thermal runaway and cell damage), the BMS will cut the charge connection to the battery with all of the other cells possibly well below their full charge potential.
Strict "Cell matching" is fundamental to the superior quality of Radenite batteries. It improves and maximises the capacity performance of the battery and prolongs service life.
Testing thousands of individual cells and recording data such as voltage and internal resistance can be a very time-consuming and thus expensive exercise. Radenite invested in creating test data sets for image recognition of li-ion cells. This process involved training a neural network on 100s of images of li-ion cells. Now, cameras fitted to robotic arms can identify, pick and test lithium ion cells automatically. It's impressive to watch a technician open a box of 100 new cells and place it on the workstation, whereon the robot arm "sees" the cells and starts to use its suction cup to left each cell from the box, take measurements and place it next to other matched cells to await welding.
Matched cells are mounted in a lattice ABS plastic framework. This provides venitlation between cells as well as structural integrity for the battery that doesn't rely on inter-cell welded connections for strength. Inter-cell connections using pure nickel connector strips are spot-welded to cell terminals. Depending on the battery, BMS sense/drain wires are either JST™ connections from a BMS or soldered to the BMS weld points. No solder is used directly on cells.
Appropriate AWG-guage heat-resistant silcone-insulated wire is used to connect the charge and discharge ports to the BMS. BMS voltage sense wires are connected to the battery via individual welded nickel connection tabs. Each tab is protected with shrink tubing. Connections to the BMS load and charge wires are soldered. The wire from the BMS to the battery -ve terminal is soldered to nickel connection tabs which are then spot welded via nickel tabs to the battery -ve cell(s). If the battery is a model that includes additional thermal protection, then a 10KΩ NTC thermistor is inserted into the centre of the pack and a third wire is added to the BMS for thermal cut-out management. Radenite uses NTC thermistors with a β (Beta) value of 3950.
After preliminary assembly, each battery is charged to ensure that it is able to reach full pack voltage/capacity and verify that the BMS cuts the charge and loads at the required threshold protecting the battery and the user. The discharge (load) terminals are short-circuited to verify the BMS protection circuitry activated. The BMS is then reactivated by applying the battery's charge voltage across to the charge terminals. Finally an electronic load tester is then used to drain the fully charged battery at the maximum current rating to ensure the battery stays within safe operating limits.
Following successful testing, the battery discharge and/or charge cables are secured internally with cable ties. Exposed nickel connection tabs are insulated and the cell terminals are covered in adhesive battery insulating material. Finally battery specification and warning labels are applied, specifying safety and usage information and its operating limits along with our contact details.
Radenite's approach to lithium-ion battery technology can be characterised by quiet innovation and steadfast commitment to performance and safety. Our Programmable Charge Voltage Supervisor Circuit is a thoughtful innovation designed to enhance both safety and efficiency in charging.
Complementing this, our Bluetooth Low Energy Battery Management Systems based on our in-house designed circuitry and PCBs offer a discreet yet effective method for managing battery health, accessible conveniently via smart devices.
Many product manufacturers encase their batteries in unique non-standard and proprietary injection-moulded enclosures, creating a dependency that can limit options. At Radenite, our comprehensive in-house 3D design and photopolymerisation manufacturing capabilities can empower clients to overcome this limitation. Partnering with us unlocks the door to superior performance batteries and freedom from the constraints of expensive proprietary options.
In our pursuit of efficiency and quality, we have embraced artificial intelligence, training image neural networks on our own GPUs for meticulous robotic recognition and testing of li-ion cells prior to battery assembly. This automated testing reduces costs and improves quality through enhanced and consistent cell-matching accuracy, a crucial element of a high-performance battery that's built to last.
Responding to the diverse needs of our clients, we have developed a range of waterproof li-ion batteries, ensuring reliability and longevity under extreme adverse conditions. A custom request from Coventry University to supply waterproof li-on batteries to provide on-board power for the CPUs in their world-beating autonomous yacht led to many successful natural and synthetic treatments to prevent battery water ingress, that far exceed the provisions of IP65.
Radenite's commitment to contuinous innovation and investment in UK battery technology to enhance safety and performance is unrivalled.
Founded in Coventry England, Radenite started manufacturing batteries in 1898 and a year later a Sunbeam car was one of the first automobiles to be fitted with a battery; a Radenite battery.
Radenite is the oldest extant battery brand in the world.
If you have questions that are not addressed by the content on this site or would like to discuss a custom battery design, please get in touch.